Core Drilling
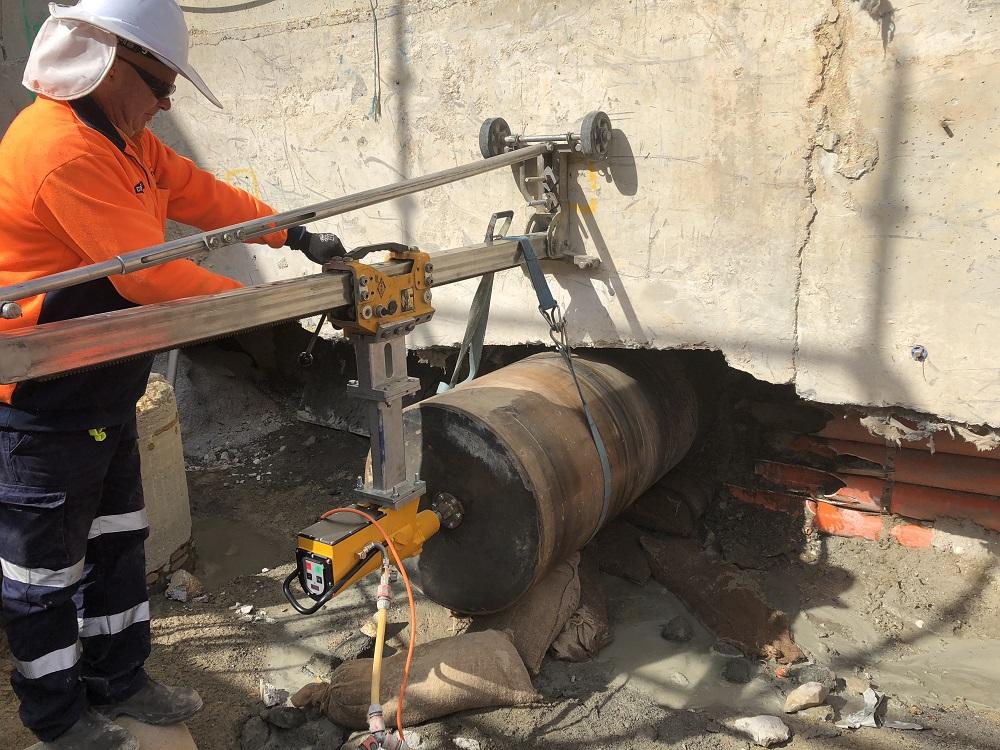
What is Core Drilling?
Concrete core drilling (also known as concrete coring) is the mechanical process of drilling a precise circular hole in concrete structures such as walls and floors. It involves the use of a core bit attached to the end of a core drill to perform the cutting. Diamond tipped segments placed at the end of a core bit perform the cutting as the core bit spins or rotates whilst making contact with the surface to be cut.
Core drilling is suitable for drilling holes through concrete, masonry, asphalt, stone, or other solid surfaces. Core holes are able to be drilled horizontally, vertically inverted, or angled.
The core bit removes approximately 4mm of the material which is cut by the segments of the core bit during the drilling process. The inner section that becomes free is known as a core, hence the reason drilling of this nature is known as "core drilling".
Core Drilling Applications
- Safety rails and fencing
- Anchoring bolts, dowel bars and lifting points
- Securing benches and tables in restaurants and locker rooms
- Signage posts, bollards, etc
- Electrical wiring, conduits, ducting, and pipes
- Plumbing, sprinklers systems, and pipes
- Retrieving core samples for analysis of material
- HVAC installations
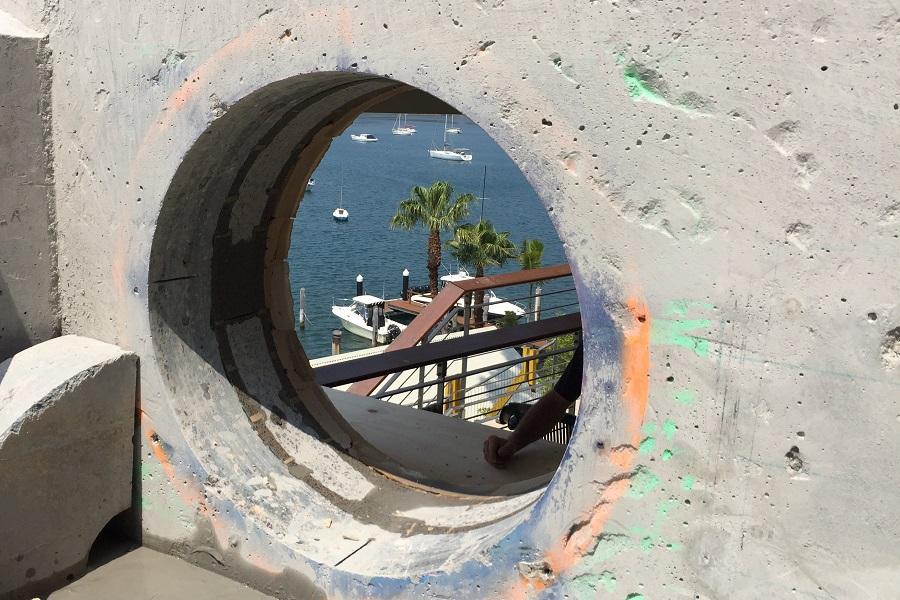
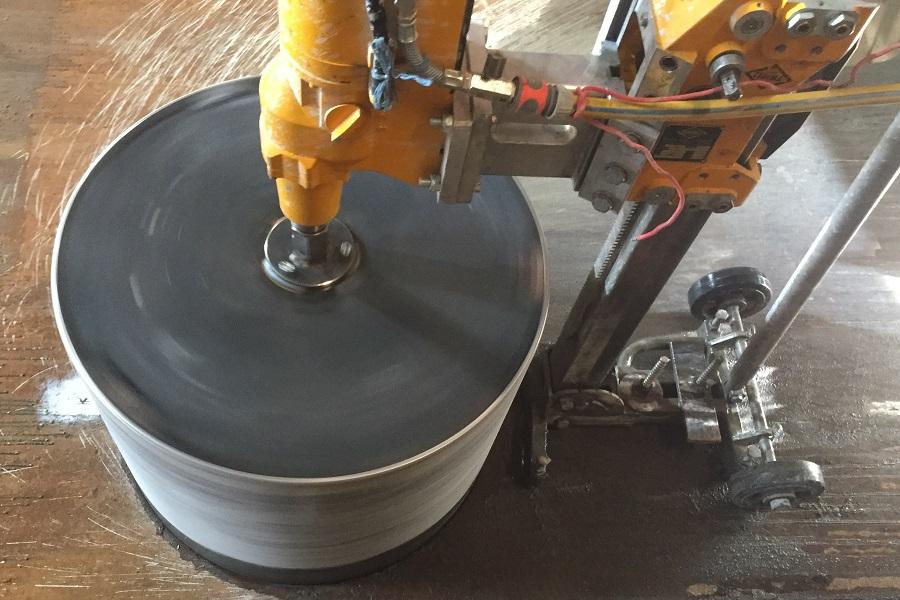
Benefits of Diamond Drilling
- Unlike percussion tools (like hammer drills), minimal noise or vibration is omitted or transferred to the surrounding area or structure when using a core drill.
- Precise and accurate hole penetration, resulting in minimal if any rectification works post penetration.
- Able to cut through steel reinforcement, where required.